

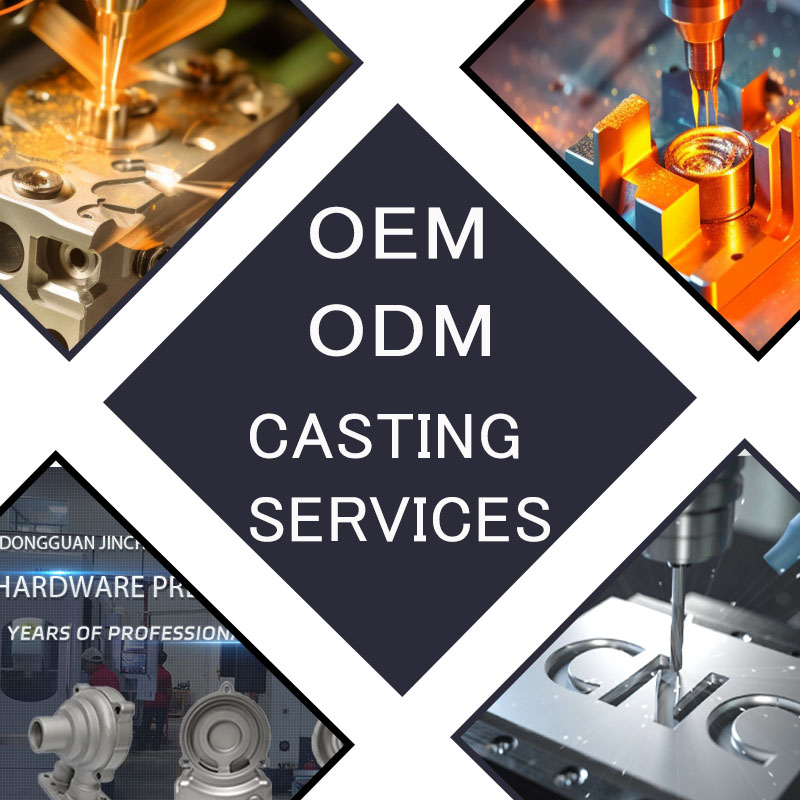
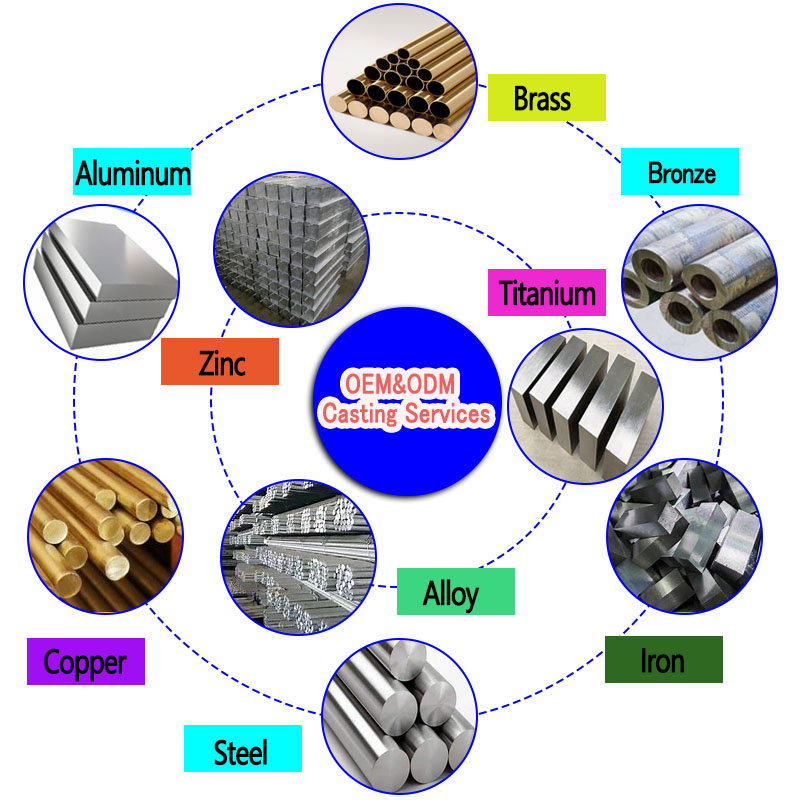
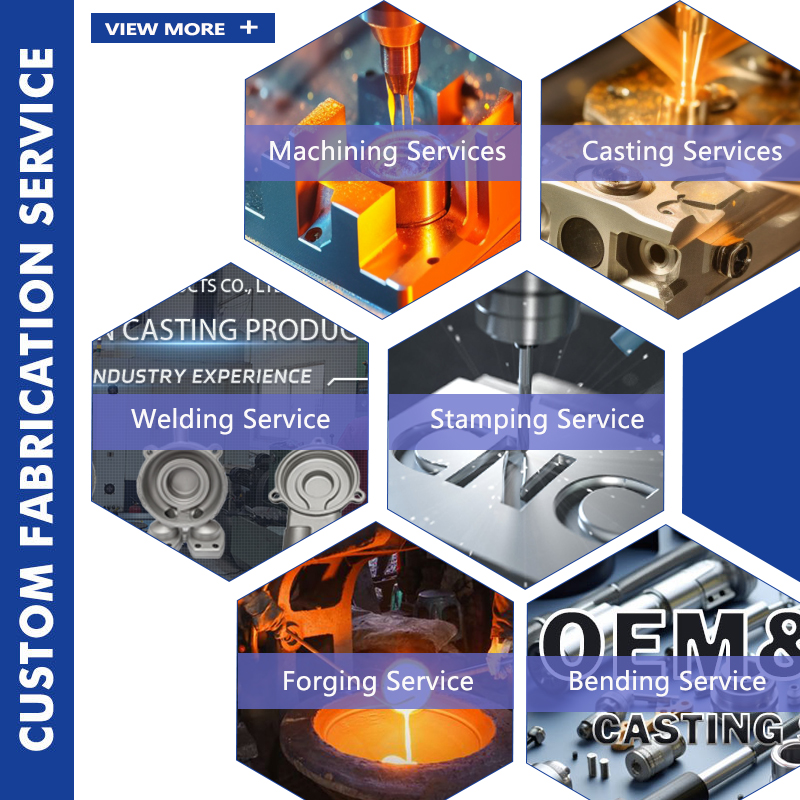
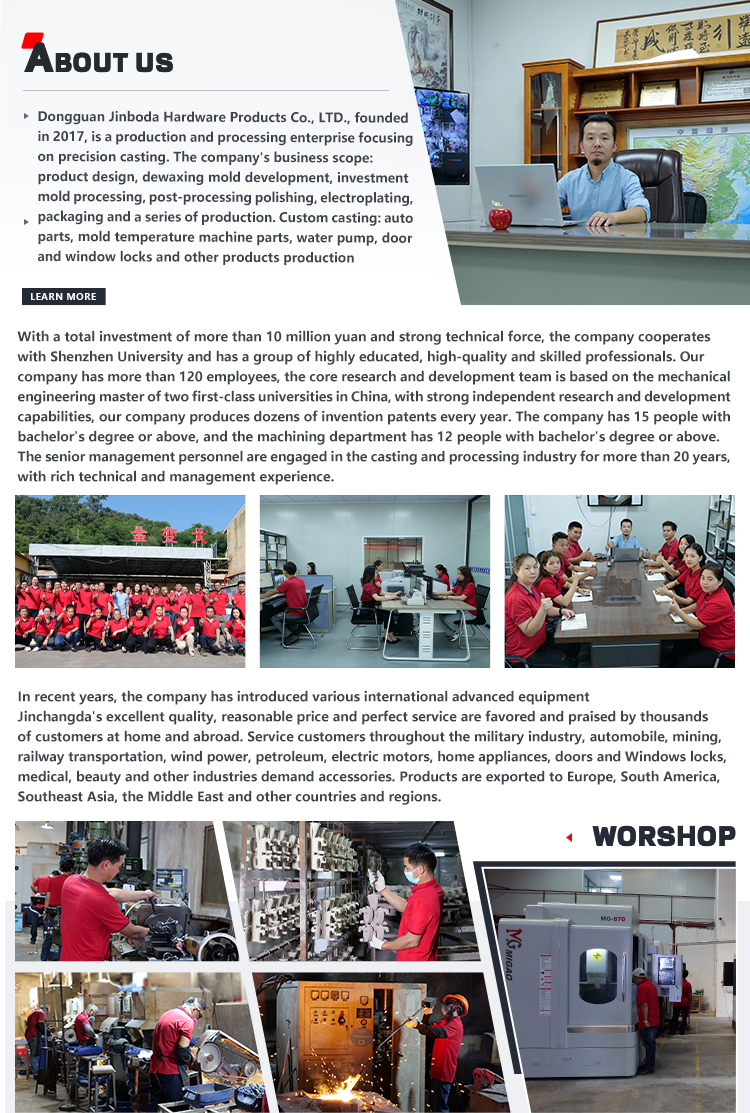
The future of casting in the building machinery industry looks promising with the continuous advancements in technology. New casting materials and processes are being developed to improve the quality, performance, and sustainability of building machinery. For example, the use of composite materials in casting may offer enhanced properties such as higher strength-to-weight ratios and better corrosion resistance. Additive manufacturing techniques are also being explored for casting, which could enable the production of more complex and customized parts. Additionally, there is a growing focus on environmental sustainability, with efforts to reduce waste and energy consumption in the casting process. The future of casting will likely involve a combination of these innovations to meet the evolving needs of the building machinery industry.
Casting and the Safety of Building Machinery
The quality of castings is directly related to the safety of building machinery. Components that fail due to poor casting quality can lead to serious accidents on construction sites. For example, a defective casting in a braking system or a lifting mechanism can cause the machinery to malfunction. Therefore, strict quality standards and testing procedures are in place to ensure the integrity of cast parts. Manufacturers need to adhere to these standards to produce reliable castings. Additionally, proper design and engineering of cast components, taking into account factors such as stress distribution and load-bearing capacity, are essential for ensuring the safety of the building machinery. Regular inspections and maintenance of cast parts are also crucial to detect and address any potential safety issues.
Casting and the Cost Efficiency of Building Machinery Production
Casting can have a significant impact on the cost efficiency of building machinery production. While the initial investment in casting equipment and molds may be relatively high, it can lead to cost savings in the long run. Mass production of cast parts using efficient casting processes can reduce the per-unit cost. Additionally, the ability to produce complex parts in a single operation can save on assembly costs. However, careful cost management is required, including optimizing the casting process to reduce waste and energy consumption, and selecting the appropriate casting method and material based on cost-benefit analysis. By balancing the quality and cost aspects, casting can contribute to the overall economic viability of building machinery production.
Casting in the Production of Earthmoving Equipment Components
Earthmoving equipment such as bulldozers and excavators rely heavily on casting for their component manufacturing. The tracks, buckets, and drive gears are often made through casting processes. Cast steel or iron is commonly used for these components due to their high strength and wear resistance. The casting process allows for the production of large and complex shapes that are essential for the functionality of earthmoving equipment. The quality of the castings directly affects the performance and durability of the equipment in tough working conditions. Manufacturers need to ensure proper casting techniques and quality control to produce reliable components for earthmoving equipment.


